A validação de limpeza é uma exigência das boas práticas de fabricação de
medicamentos, requerida por organismos regulatórios locais e internacionais. É de
responsabilidade da indústria validar e documentar seu processo/procedimento de
limpeza garantindo assim sua confiabilidade e reprodutibilidade, demonstrando que
seu procedimento de limpeza é eficaz e remove resíduos dos produtos, agentes de
limpeza e microbiológicos a níveis pré-determinados de aceitação.
A ideia da validação é que se um procedimento de limpeza for mal executado, resíduos podem contaminar o próximo lote do produto a ser fabricado (subsequente) podendo gerar prejuízo à saúde do paciente que eventualmente venha utilizar este medicamento para uma terapia farmacológica.
E em termos de resíduos contaminantes, estamos falando no produto anterior/insumo farmacologicamente ativo (IFA), ou ainda residuais de agentes de limpeza (detergente e sanitizante), carga microbiana não removida, além de solventes, produtos de degradação, ou ainda outros materiais (partículas, poeiras, lubrificantes, excipientes, dentre outros). Para se evitar tais contaminações, processos de limpeza robustos e validáveis de equipamentos e utensílios são essenciais para garantir a segurança dos medicamentos produzidos.
Estratégias iniciais da validação de limpeza

A estratégia da condução dos estudos de validação de limpeza, se mal definida, pode impactar em uma maior demanda do tempo para a sua conclusão, e também em custos elevados.
Neste sentido, pode-se adotar algumas estratégias para otimizar a validação de limpeza que serão listada a seguir. No entanto, vale ressaltar que a estratégia a ser adotada deve ter como base a análise dos riscos, sendo esta executada tanto pelo Gerenciamento de risco de compartilhamento de área produtiva quanto o próprio gerenciamento de risco dos estudos de validação de limpeza.
A abordagem tradicional das validações, incluindo os processos de limpeza, preconiza a realização de no mínimo três corridas consecutivas do pior caso. Esta estratégia está baseada em fundamento estatístico, além de ser uma definição preconizada pelas indústrias e o setor regulador. No entanto, a prática tem demonstrado que resultados satisfatórios de três corridas somente, não são suficientes para garantir a consistência do processo (SINDUSFARMA, 2018 e IN 47, 2019). Nesse sentido, a avaliação do risco promove embasamento para maior confiabilidade da quantidade de lotes a serem acompanhados.
Dentro da validação de limpeza há outros estudos relevantes como: A influência do tempo entre a fabricação e a limpeza e o tempo entre a limpeza e o uso, que deve ser levada em consideração para definir tempos de limpo e sujo do equipamento para posterior utilização ou processo de limpeza. E a fabricação da campanha, produção consecutiva de vários lotes do mesmo produto, com realização ou não de uma limpeza parcial entre lotes e limpeza completa ao término (IN 47, 2019 e PICS, 2018).
Holding time da validação de limpeza
Tempo de sujo
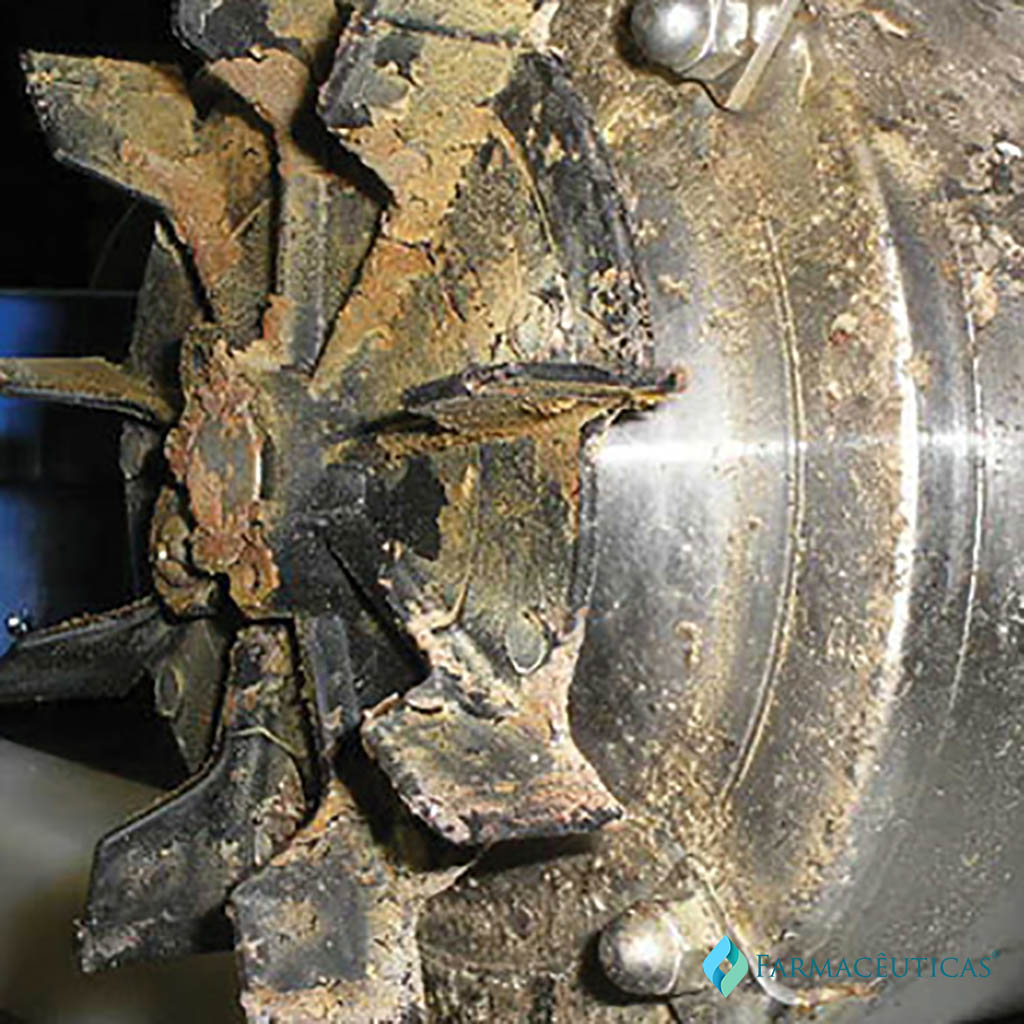
O objetivo da validação do tempo de sujo consiste no tempo em que o
equipamento pode permanecer sujo após final de produção sem exceder os níveis de
aceitação microbiológicos.
Neste tipo de estudo é importante destacar a necessidade de avaliação microbiológica e da formação de produtos de degradação.
Tempo de limpo
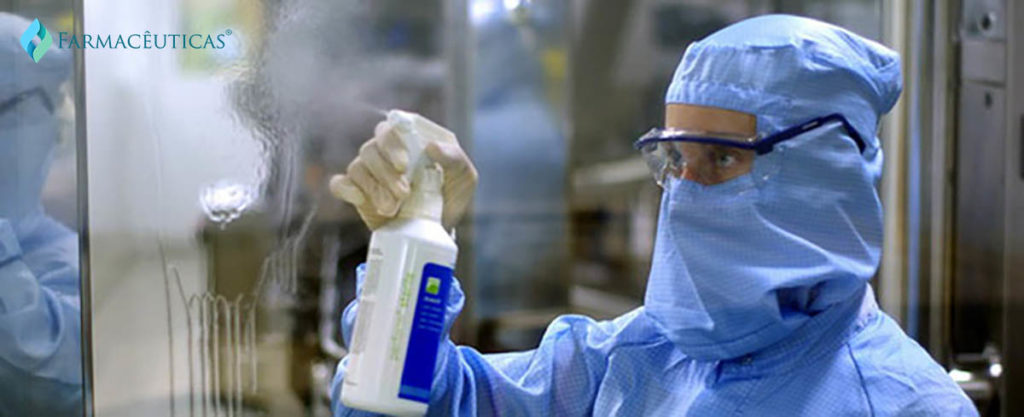
No caso da validação do tempo de limpo, verifica-se o tempo no qual o equipamento se mantém limpo a níveis aceitáveis de resíduos microbiológicos. Ou seja, é a eficácia do sanitizante por um tempo definido como “tempo de limpo” em que o equipamento pode aguardar após ser limpo até a próxima utilização sem riscos de contaminação para a próxima produção.
Para este tipo de abordagem, apenas a avaliação microbiológica é suficiente.
Validação de lotes em campanha
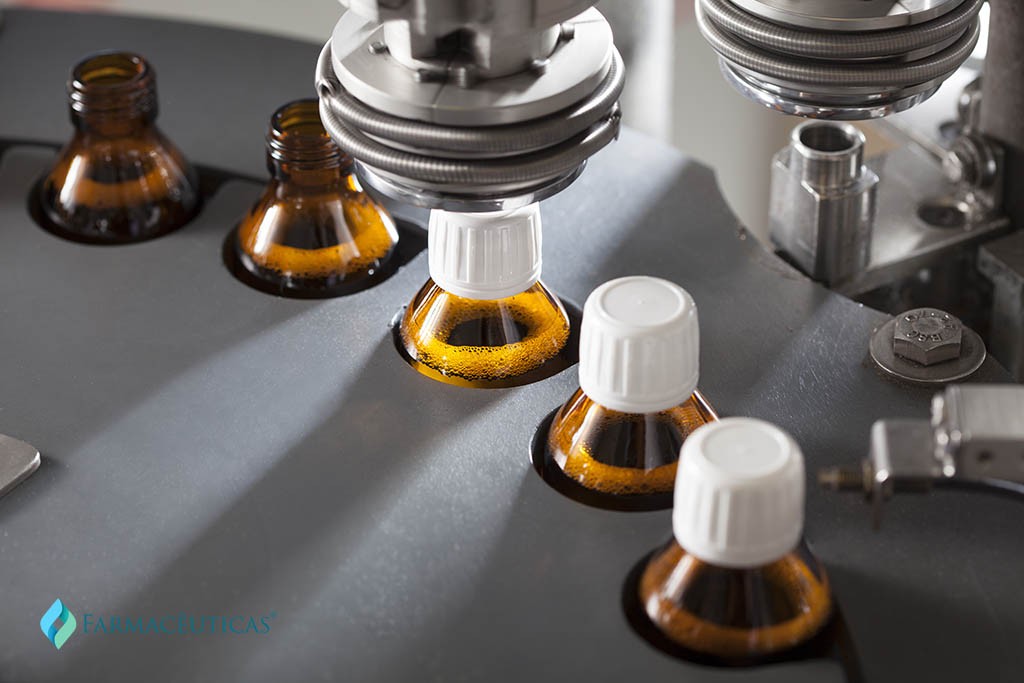
Já a validação de campanha é o tempo e a quantidade de lotes de um mesmo
produto produzido em batelada, sendo feita ou não uma limpeza parcial (normalmente
a seco), sem riscos de contaminação entre lotes e sem riscos de formação de produtos de
degradação.
Lembrando que o número de horas produtivas deve ser igualmente validado, assim como a qualidade dos lotes produzidos em campanha atestados.
E em termos de estratégia, o melhor cenário é validar os tempos de limpo e de sujo após a campanha, uma vez que esta seria a pior condição para acúmulo de resíduos.
E para saber mais sobre o assunto, leia o artigo:
Estratégias da validação de limpeza
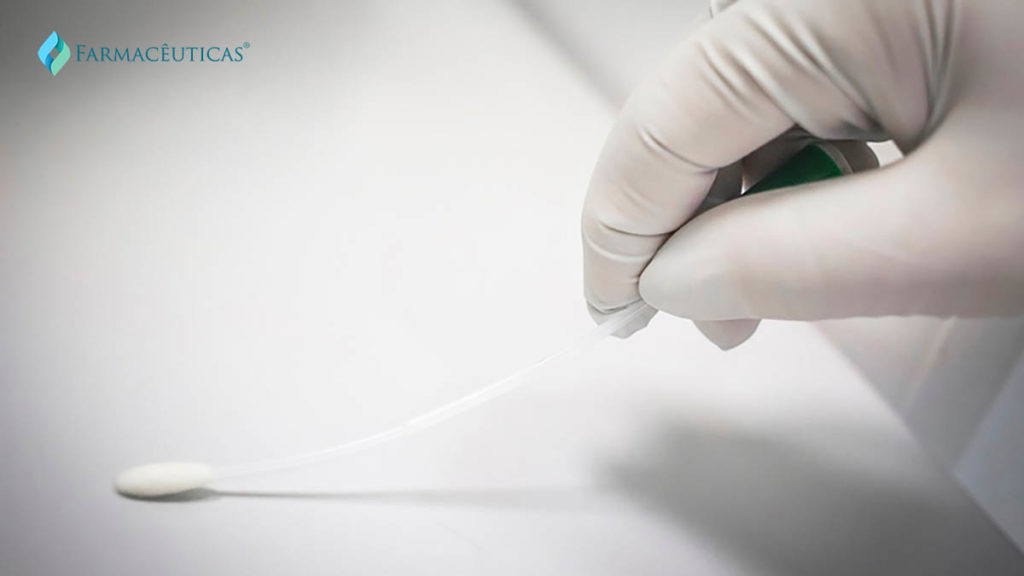
Para escolha da estratégia para validação de limpeza, a indústria deve definir
quais as diretrizes para suprir sua demanda:
- Validação de limpeza por rota dedicada
- Validação de limpeza por rota compartilhada (multi-propósito)
- Validação de grupos de equipamentos
- Validação individual por equipamento
Mas como definir se uma linha de deve ser dedicada ou compartilhada?
Para que esta definição seja segura deve ser feito por meio da avaliação do risco, ou seja, avaliação dos efeitos críticos e valores de PDE obtidos nos relatórios específicos dos produtos/IFAS produzidas na área ou linha avaliada e mitigação dos riscos por meio do Gerenciamento de Risco de Compartilhamento de área produtiva.
Caso queira mais informações sobre o assunto, recomendamos a leitura do artigo:
Ou assista ao vídeo:
Após a definição baseada em risco, a empresa deve:
- Elaborar a matriz de equipamentos x produtos e entender as diferentes rotas produtivas.
- Verificar se existe de fato um produto definido como pior caso para uma ou mais linhas
- Caso seja identificado que cada equipamento tem um pior caso, definir os possíveis agrupamentos de equipamentos.
- Definir o pior caso por equipamento, ou linha.
- Definir o pior subsequente (matemático)
Lembrando que a avaliação das possibilidades de agrupamentos de equipamentos deve ser feita por meio de racional científico, ou seja, da evidência da similaridade para a validação de limpeza.
1. Linha dedicada
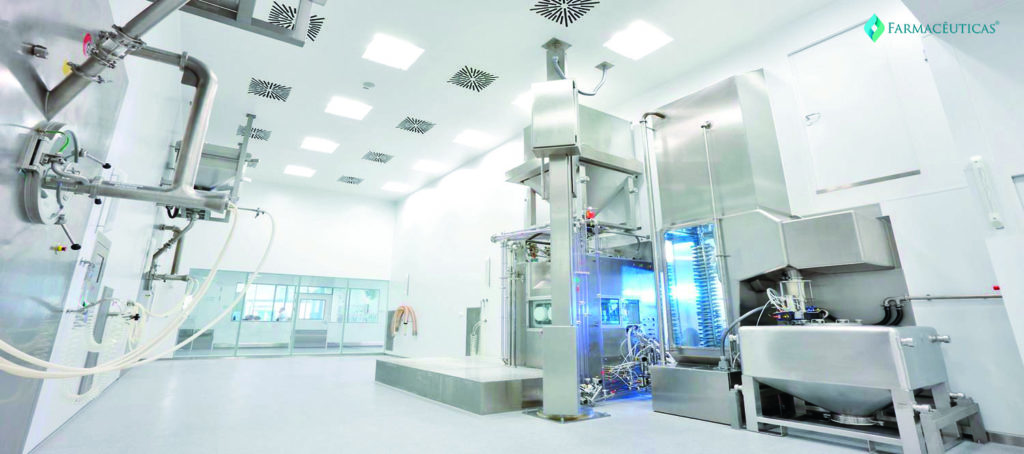
Aqui não há a necessidade de escolha do pior caso, pois é fabricado um único produto, podendo este ter diferentes dosagens. Mas a necessidade da avaliação do residual da substância ativa ainda continua, isso porque temos a possibilidade de acúmulo do IFA.
Então, para quem realiza a amostragem apenas de detergente e micro em linhas dedicadas, é melhor ir repensando a estratégia. Isso porque a amostragem e análise de residual do ativo vem sendo requerida mesmo para linhas dedicadas.
2. Validação de limpeza por linha ou rota produtiva
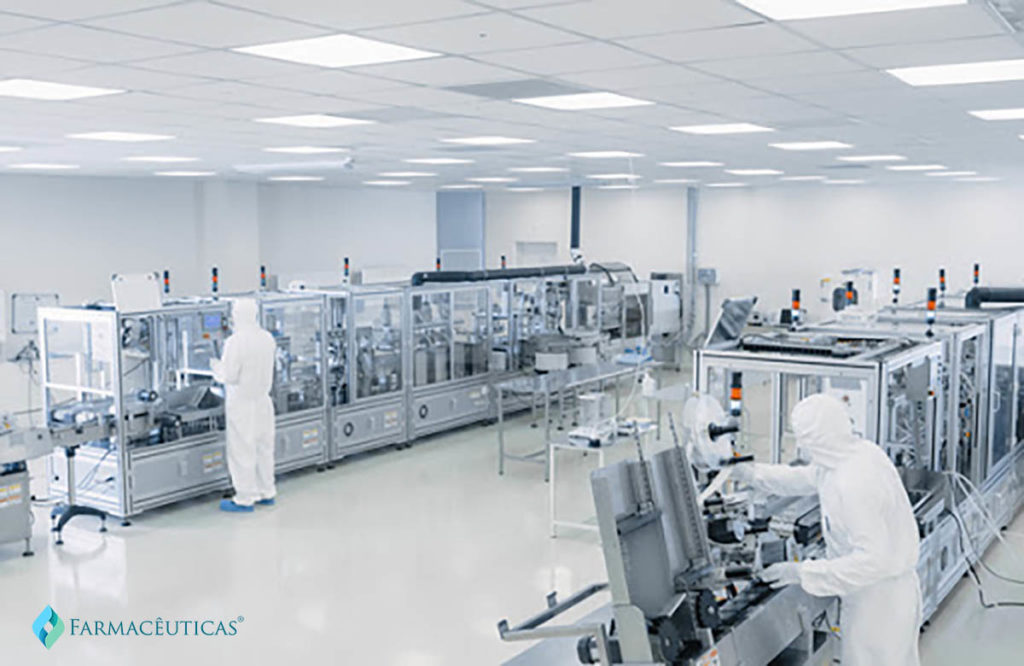
Nesta estratégia não há necessidade do agrupamento de equipamentos/utensílios. Valida-se um único produto selecionado como “pior caso” em única rota produtiva englobando todos os equipamentos envolvidos no processo produtivo.
A vantagem desta estratégia é que temos apenas um único protocolo e relatório, e todos os equipamentos da rota constam em uma única validação.
Mas é importante que a equipe de validação e do controle de qualidade estejam alinhadas visto a quantidade de amostras, quase que simultâneas, que serão retiradas para análise.
A desvantagem é que se entrar um produto novo sendo este elegido como novo pior caso, e este entrar somente em alguns dos equipamentos, ou até mesmo em um único, e não nos demais da rota produtiva, a validação da linha pode ser perdida.
3. Estratégias de agrupamentos de equipamentos
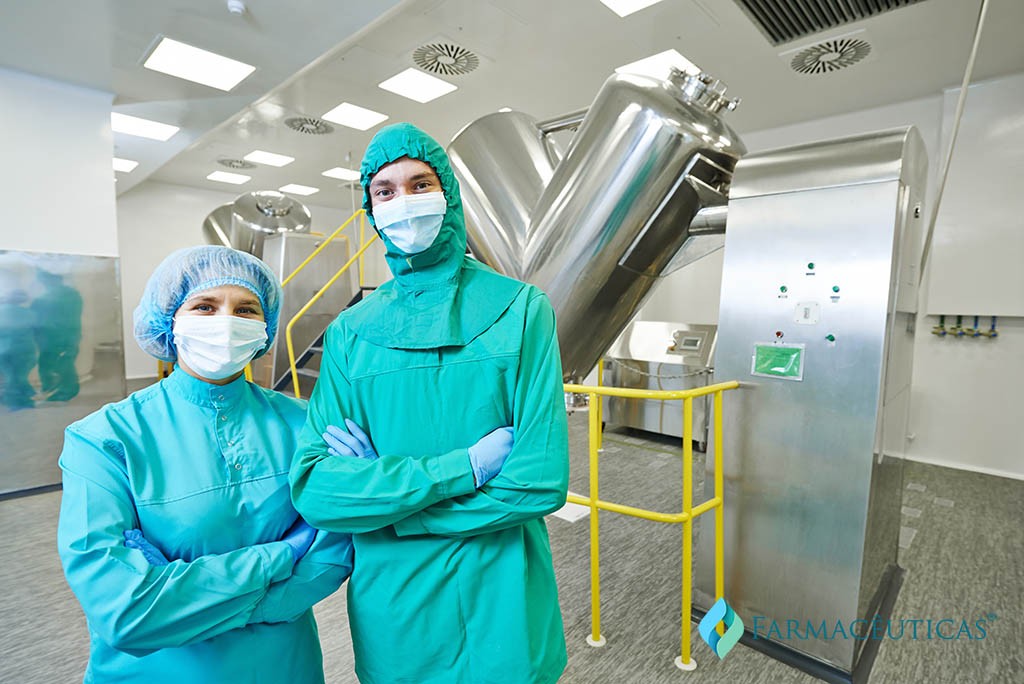
Nesta situação, não é possível definir um pior caso para uma rota produtiva inteira. Na matriz de produtos x equipamentos há diversas possibilidades de compartilhamento e cada equipamento possui um pior caso diferente.
Mas aqui torna-se possível a utilização de agrupamentos de equipamentos e escolha
do produto “pior caso” único para um conjunto de equipamentos comprovadamente similares.
Mas é importante ressaltar que deve haver uma comprovação documentada desta similaridade que permita o agrupamento. Deve existir um racional científico descrito em relatório específico de similaridade de equipamento para validação de limpeza, ou mesmo a justificativa técnica deve estar descrita no protocolo. O relatório de similaridade da qualificação pode ajudar, mas ele sozinho não é suficiente para embasar. É necessário um documento específico para a validação de limpeza.
4. Validação de limpeza individual
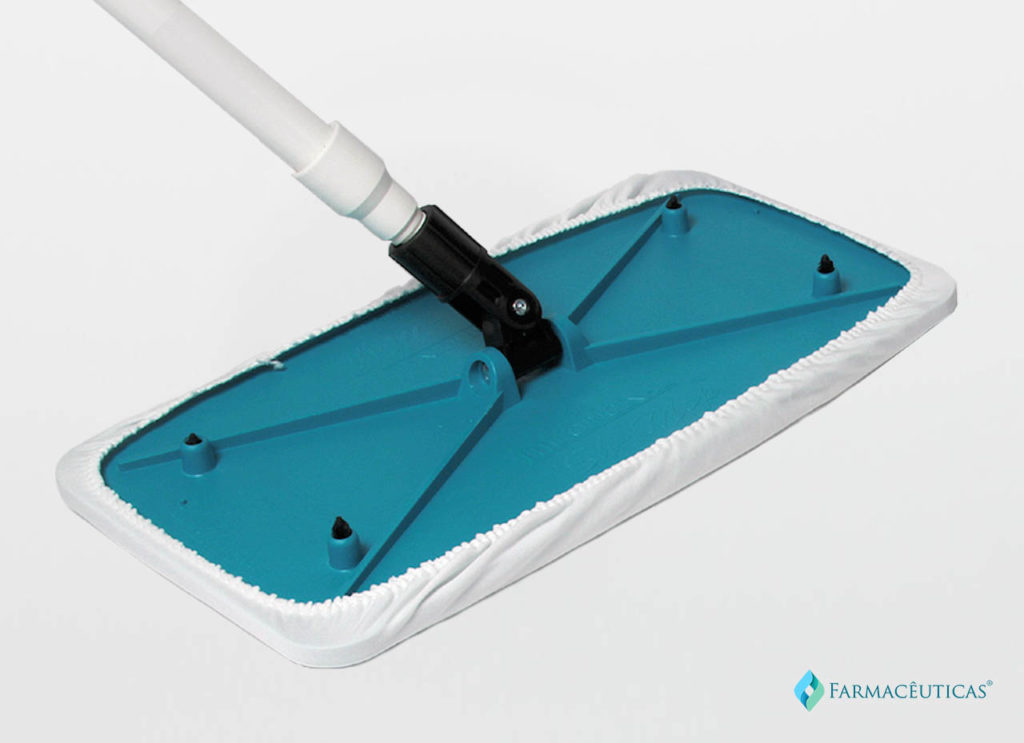
Aqui não há a possibilidade de agrupamentos de equipamentos, não é há como atestar a similaridade, ou mesmo o pior caso do portfólio de produtos que passam por ele é diferente dos demais equipamentos.
Aqui temos um protocolo/relatório único por equipamento.
Programação da validação de limpeza
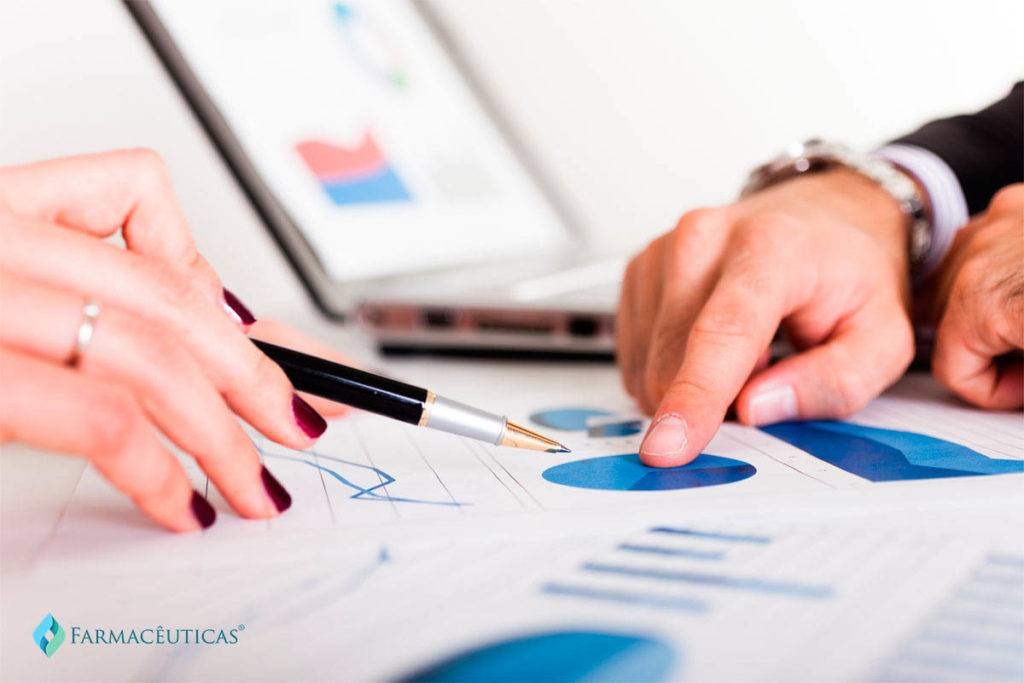
Após definição da melhor estratégia, deve-se programar juntamente com PCP e produção a entrada dos lotes que serão utilizados na validação do procedimento de limpeza, validação dos tempos de limpo e de sujo, ou até mesmo da campanha. Contemplando os intervalos de parada dos holding times da limpeza e o número de lotes de cada campanha. Todos os tempos de parada e condições a serem replicadas (em triplicata…) devem ser detalhadamente pensadas e acordadas para que não haja “furo” na validação de limpeza.
Lembrando que a perda da consecutividade dos lotes é motivo suficiente para a perda do estudo como um lote, uma vez que estatisticamente é impossível comprovar a reprodutibilidade dos resultados.
Caso não seja possível contemplar o intervalo de tempo de limpo e tempo de sujo entre os lotes de validação de procedimento de limpeza, dá-se prioridade ao tempo de sujo, que deve ser feito com o produto definido como pior caso. Assim a validação do tempo de limpo pode ser feita posteriormente após limpeza da última corrida do produto “pior caso” e as demais sem resíduo do produto definido como pior caso, visto que já estará comprovado mediante validação de procedimento de limpeza que o procedimento utilizado remove resíduos de ativo, agentes de limpeza e residual microbiológico a limites acetáveis, ficando sob responsabilidade do estudo de validação de tempo de limpo a comprovação da eficácia do sanitizante utilizado.
Elaboração e revisão do artigo
Artigo elaborado por Fulvi Brito e revisado por Fernanda de Oliveira Bidoia.
Outubro de 2020
Referências bibliográfica
RESOLUÇÃO DA DIRETORIA COLEGIADA. RDC nº 301/2019 – ANVISA. Dispõe sobre as Boas Práticas de Fabricação de Medicamentos
INSTRUÇÃO NORMATIVA ANVISA Nº 47/2009 – Estabelece regras para elaboração, harmonização, atualização, publicação e disponibilização de bulas de medicamentos para pacientes e para profissionais de saúde.
PDA Technical Report No. 29 (Revised 2012) Points to Consider for Cleaning Validation
PIC´S – PHARMACEUTICAL INSPECTION CONVENTION PHARMACEUTICAL INSPECTION CO-OPERATION SCHEME (2018)
GUIA DE VALIDAÇÃO DE LIMPEZA PARA FARMOQUÍMICOS – ANVISA